What are the main types of mechanical seals for centrifugal pump?
Mechanical seals type in centrifugal pump
Mechanical seals are devices designed to prevent leakage of fluids between two surfaces. They are also called pump shaft seals. Mechanical seals consist of two plane surfaces placed perpendicular to the shaft. One of these surfaces is fixed onto the seal chamber housing, while the other surface, attached to the rotating shaft, acts as the primary seal. There are three main types of mechanical seals: wet seals, dry seals, and gas seals.
Wet seals are commonly used in pump system where fluids are present, such as chemical processing plants and oil refineries. They operate by creating a barrier between the two surfaces using a liquid medium, such as oil or water.
Dry seals are typically used in applications where no fluids are present, such as in vacuum pumps and steam turbines. They rely on a combination of materials, such as carbon and ceramic, to create a seal.
Gas seals, on the other hand, use a gas as the sealing medium. They are commonly used in high-speed rotating equipment, such as compressors and turbines, and offer higher efficiency and stability than other types of seals.
Here are some of the common types of seals used in industrial engineering purposes.
- Pusher&non-pusher seals
- Balanced&unbalanced seals
- cartridge seals
- Elastomer bellows seals
- Metal bellows seals
- Split seals
- Gas seals
- Single seals
- Double seals
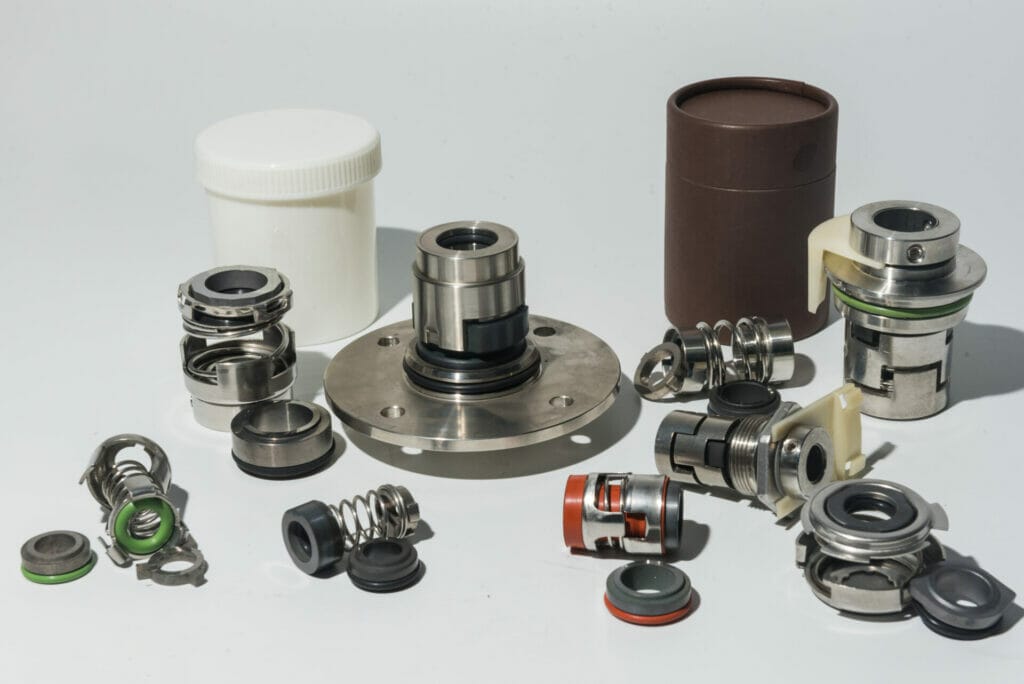
Pusher&non-pusher seals
Pusher and non-pusher seals are two types of mechanical seals that are commonly used in various applications for sealing purposes.
Pusher seals are designed with a spring-loaded mechanism that pushes the seal face against the rotating shaft. These seals are ideal for high-pressure applications, as they can maintain a constant seal face contact even when there are slight variations in the shaft movement. Pusher type seals pose a drawback wherein the elastomer below the primary seal face may degrade as the surface moves along the shaft/sleeve while in use, thereby restricting its effectiveness in sealing at elevated pressures. In pusher seals, a dynamic secondary seal moves along with the primary seal face in an axial direction.
Non-pusher seals do not use a spring mechanism and rely on the shaft movement to maintain the seal face contact. These seals may also are more suitable for low-pressure applications, as they require a certain degree of movement for the seal to work effectively. Both types of seals have their advantages and disadvantages, and the choice depends on the specific application requirements.
Balanced&unbalanced seals
Balanced mechanical seal is designed to maintain the same amount of pressure on both sides of the seal, which helps to counterbalance the effects of centrifugal force and ensure uniform wear. Balanced seals are generally used in high-speed applications, such as centrifugal pumps, because they reduce vibration and require less maintenance.
Unbalanced mechanical seals are designed to apply more pressure on one side of the seal than the other, which can cause friction and wear over time. However, they are more cost-effective and are commonly used in low-speed applications, such as mixers and agitators.
Cartridge seals
Cartridge seals incorporate all the seal components into one unit. These seals are designed to provide a secure and maintenance-free seal for pumps, mixers, and rotating equipment. The cartridge seal is made up of a rotating seal face and a stationary seal face, which come together to prevent fluid leakage.
They are widely used in a variety of industries, including chemical processing, pharmaceuticals, power generation, and petroleum. The main advantage of the cartridge seal is that it eliminates the need for complex installation and maintenance processes, making it a more convenient and cost-effective option for sealing applications.
Additionally, since the seal is fully contained in a cartridge, it offers ease of handling and reduces the possibility of errors during installation. Overall, cartridge seals have become a preferred choice for many users seeking reliable sealing solutions.

Elastomer bellows seals
Elastomer bellows seals are designed to provide an effective and reliable sealing solution in a range of industrial and commercial applications. The bellows structure of these seals allows for flexing and movement, which makes them ideal for use in dynamic applications where there is movement between two surfaces.
The elastomer material used to make these seals allows for excellent resistance to a range of chemicals and fluids, making them ideal for use in environments where there are harsh or aggressive materials. Elastomer bellows seals are also known for their ability to reduce friction and wear, which can help to increase the lifespan of the seal and reduce maintenance costs.
They are commonly used in pumps, mixers, and other fluid handling equipment, where they can effectively seal against leaks and contamination. Overall, elastomer bellows seals are a durable and efficient sealing solution that can provide reliable performance in a range of demanding applications.
Metal bellows seals
Metal bellows seals are used in various industries, including oil and gas, chemical, and petrochemical. These seals provide superior protection against leakage, making them an ideal choice for applications where high pressures, temperatures, or corrosive environments can be a problem.
Metal bellows seal consists of a thin-walled metal bellows that is formed into a series of convolutions. The bellows is then welded to the stationary and rotating seal faces, creating a hermetic seal that can handle extreme environmental conditions.
Compared to standard seals, metal bellows seals have a longer lifespan, require less maintenance, and can withstand higher pressures, making them a cost-effective solution for many industrial applications.
Split seals
Split seals are mechanical devices designed to prevent leakage in rotary equipment, such as pumps or mixers. They are also called mechanical seals or seal assemblies, and they consist of several components like the rotating seal face, the stationary seal face, and the secondary sealing elements (e.g., O-rings or gaskets).
The split seal design refers to the ability to disassemble the seal and replace the components individually, without taking apart the entire equipment or dismantling the shaft. Split seals offer several advantages over other seal types, such as reduced maintenance downtime, lower replacement costs, and improved equipment reliability.
They are commonly used in the chemical, pharmaceutical, and food industries, or wherever a high level of hygiene and cleanliness is required. Some split seal models are also designed to work in high-pressure or high-temperature environments.
Gas seals
Gas seals are essential components in many industrial applications, including pumps, compressors, and turbines. They are designed to prevent gas leakage between two surfaces and maintain contact between the sealing surfaces during operation.
The sealing mechanism of gas seals relies on the pressure difference between the internal and external environments of the system. Gas seals can be classified into two types: dynamic and static.
Dynamic seals are used in high-speed applications where there is relative motion between the sealing surfaces. Examples of dynamic seals include labyrinth and carbon seals.
Static seals, on the other hand, are used in low-speed applications where there is no relative motion between the surfaces, such as O-rings and gaskets.
Proper selection, installation, and maintenance of gas seals are important to ensure efficient operation, minimize losses, and prevent the release of harmful gases into the environment.
Single seals
Single seals are devices that are designed to prevent leakage of fluids from pumps or other industrial equipment. They consist of two sealing surfaces that come into contact with each other and create a barrier that prevents the fluid from escaping. One of these surfaces is stationary while the other is attached to the rotating shaft of the equipment. The stationary surface is usually made of a harder material such as ceramic or tungsten carbide, while the rotating surface is made of a softer material such as carbon.
Mechanical seals are commonly used in applications that involve high pressures, high temperatures, or aggressive fluids. They can provide reliable and long-lasting sealing performance in a wide range of industrial applications. However, their installation and maintenance can be challenging, requiring specialized skills and tools.
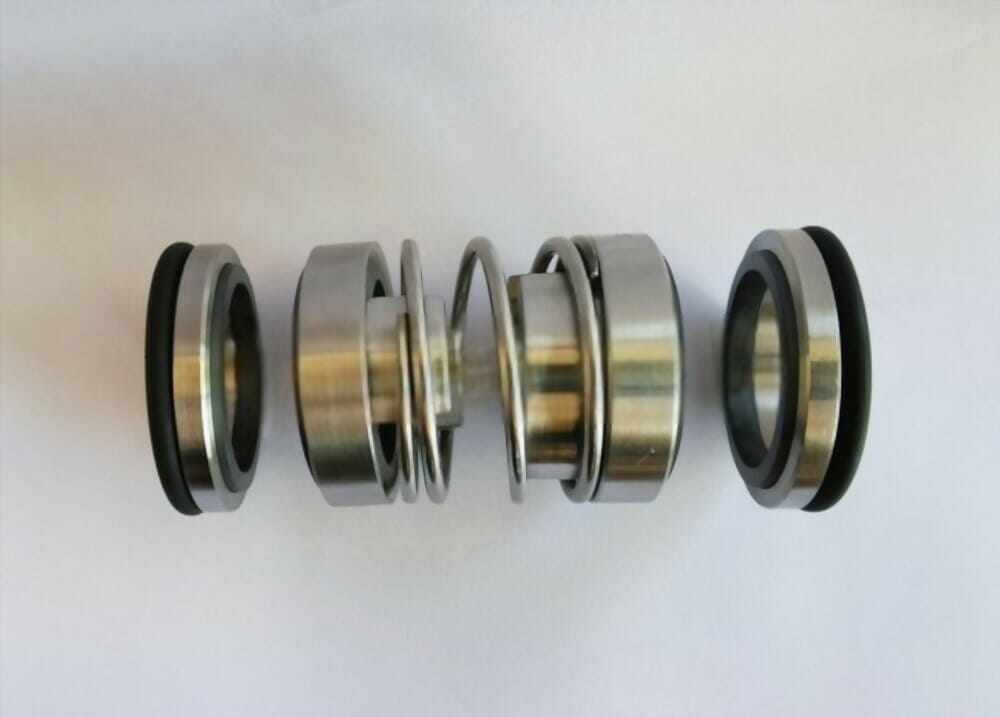
Double seals
Double seals are a type of sealing mechanism that is commonly used in rotating measurement equipment such as pumps and mixers. They are designed to provide a high-performance barrier against leakage of fluids and gases in situations where it is critical to prevent contamination or loss of materials.
Double seals consist of two sets of rotating seals and stationary faces, with an interstitial space between them filled with a fluid such as water, oil or a nitrogen gas. The design’s unique dual seal feature makes it highly reliable and effective in resisting pressure and temperature changes. Additionally, the interstitium between the two seals also permits detection of any signs of leakage which prevents further damage to the equipment until repairs can be made. Double mechanical seals are the preferred choice for a wide range of applications involving hazardous, corrosive, or high-pressure fluids that require reliable protection against leaks.
Choosing the perfect type of mechanical seal for centrifugal pump: factors to consider
When choosing mechanical seals for centrifugal pumps, there are several important factors to consider. It is important to select the right seal for the job in order to ensure optimal performance and prevent future problems.

1. Application Requirements
The first factor to consider when selecting a pump seal is the application requirements. It’s important to understand what you need the seal to do and how it will be used in order to make sure you get the right product.
You should consider if there are any hazardous materials, corrosive chemicals or high temperatures that could affect the performance of the seal, as this can influence your choice. Also take into account other environmental factors such as dust and debris which may require additional protection for your machine components or need a different type of material for the seal itself. You’ll also want to think about maintenance needs – will frequent inspection and replacement be easy? And finally, look at compatibility with existing parts and systems so there won’t be any surprises further along down the line.
2. Pressure Rating
The pressure rating of a mechanical seal is one of the most important factors to consider when choosing it, since it will directly influence its performance and durability. The higher the pressure rating, the better chance it has of lasting longer in harsh environments. Pressure ratings are usually determined by how much force can be applied to a particular seal before it fails or starts leaking. A good rule of thumb is that seals with higher pressure ratings typically cost more than those with lower ones, but they offer superior performance and longevity for applications operating at high pressures. When selecting a mechanical seal for your application, make sure to choose one that meets the specific requirements for both maximum working and burst pressure.
3. Speed Of Rotation
When it comes to choosing a mechanical seal, the speed of rotation must be carefully considered. Mechanical seals are used in applications that involve rotating equipment, such as pumps or motors. The rotational speed of the equipment will determine which type and size of seal is required.
It’s important to ensure that the seal you choose can handle the necessary speeds without damaging itself or any other parts connected to it. Factors like temperature and pressure also come into play when selecting a mechanical seal for a particular application. Be sure to consult with experts if you’re unsure about what type of seal is best suited for your needs!
4. Temperature Range
Temperature range is an important factor to take into consideration when choosing a mechanical seal. If the temperature of the fluid being sealed is too hot or too cold, it can damage the seal and cause it to leak. It’s important to know what temperatures your application will be working in so you can select a seal that has the proper temperature rating for your needs.
You should also consider any potential fluctuations in temperature you may experience in your system as this can have an effect on how well your mechanical seal performs over time. If there are wide swings in temperature, look for a seal that has been designed with flexibility and resilience to handle those fluctuations without compromising performance.
5. Compatibility
One of the most important factors to consider when choosing a mechanical seal is compatibility. The components of the seal must be compatible with each other to ensure that it will work properly and provide a reliable seal. It is important to know what type of media you are dealing with, such as water, oil or gas, so that you can choose a seal material that is compatible with your medium.
In addition, it is also important to consider if the rotating parts are compatible with the shaft size and surface finish. If there are any inconsistencies between these two aspects, then it is likely that friction will occur which can lead to poor performance and even failure of the entire system.
Conclusion
Choosing the correct seal for your application is essential for ensuring the safety and longevity of your equipment. By considering the factors outlined in this article, you can be sure that you will make a well-informed decision when selecting a seal.
It’s important to remember that seal life is designed to last long, so don’t be tempted to choose one just because it is cheaper; instead, take into account all of the factors discussed here and ensure that you select a high quality product which meets all of your needs.
Finally, always make sure that you use correct installation techniques and procedures in order to maximize the life expectancy of your mechanical seal. With these tips in mind, you can rest assured that any mechanical sealed system will work perfectly for years to come!